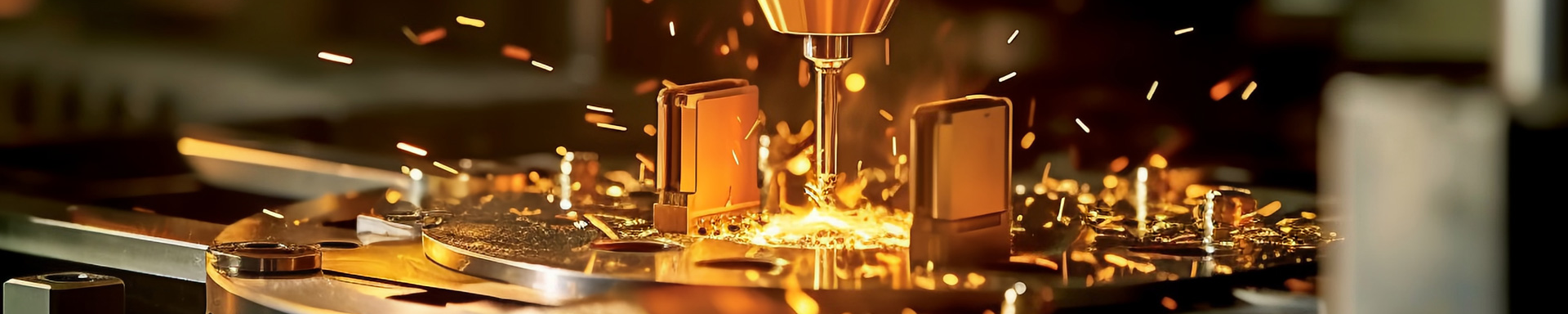
Fortgeschrittene Techniken im Automobil-Druckguss
2024-11-22 15:41Verbesserungen beim Hochdruckguss (HPDC)
Das Druckgießen (HPDC) ist nach wie vor ein Eckpfeiler der Automobilkomponentenproduktion und wird für seine Geschwindigkeit und die Möglichkeit, komplexe Teile herzustellen, geschätzt. Beim herkömmlichen HPDC-Verfahren ist es jedoch oft schwierig, bei großen Chargen eine gleichbleibende Maßgenauigkeit und Oberflächenqualität zu erreichen. Moderne Verbesserungen konzentrieren sich auf die Optimierung des gesamten Prozesses, von der Formkonstruktion und Materialauswahl bis hin zu Einspritzparametern und Nachbearbeitungstechniken. Dazu gehören Fortschritte bei Formmaterialien, die eine höhere Verschleißfestigkeit und bessere Wärmeübertragungseigenschaften bieten, was zu einer längeren Formlebensdauer und einer verbesserten Teilequalität führt. Darüber hinaus ermöglicht die Implementierung hochentwickelter Steuerungssysteme eine präzise Überwachung und Anpassung von Parametern wie Einspritzdruck, Geschwindigkeit und Haltezeit, wodurch Abweichungen minimiert und gleichbleibende Ergebnisse sichergestellt werden.
Ein weiterer wichtiger Verbesserungsbereich ist der Einsatz von Simulationssoftware. Diese fortschrittlichen Programme ermöglichen es Ingenieuren, verschiedene Formendesigns und Einspritzparameter virtuell zu testen, bevor die eigentliche Produktion beginnt. Diese Vorhersagefähigkeit reduziert den Bedarf an kostspieligen physischen Prototypen und Iterationen erheblich, beschleunigt den Entwicklungsprozess und minimiert den Abfall. Die Integration hochentwickelter Sensoren in die Druckgussmaschine liefert Feedback in Echtzeit, wodurch die Prozesskontrolle weiter verbessert und das Ergebnis optimiert wird. Dieser datengesteuerte Ansatz führt zu erheblichen Verbesserungen der Teilequalität, reduziert Defekte und erhöht die Gesamteffizienz.
Dünnwand-Druckguss
Die Nachfrage nach Leichtbaufahrzeugen führt zu einem starken Trend zum Dünnwand-Druckguss. Diese Technik ermöglicht die Herstellung von Bauteilen mit deutlich reduzierter Wandstärke bei gleichzeitiger Beibehaltung der strukturellen Integrität. Dies trägt nicht nur zur Gewichtsreduzierung bei, sondern senkt auch die Materialkosten. Dünnwand-Guss erfordert jedoch eine präzise Kontrolle des Spritzvorgangs und den Einsatz spezieller Gussformen. Moderne Techniken nutzen optimierte Gussformdesigns mit verbesserten Kühlsystemen, um eine schnelle Erstarrung zu gewährleisten und Defekte wie Porosität oder Verformungen zu vermeiden. Die Entwicklung hochfester Aluminiumlegierungen, die speziell für Dünnwandanwendungen geeignet sind, verbessert die Machbarkeit und Festigkeit dieser Bauteile zusätzlich.
Der Prozess profitiert auch von Innovationen im Matrizendesign, die Funktionen wie optimierte Angusssysteme und Entlüftungsstrategien integrieren, um den Metallfluss zu verbessern und Lufteinschlüsse zu minimieren. Fortschrittliche Simulationen spielen eine entscheidende Rolle bei der Vorhersage potenzieller Probleme und der Optimierung der Prozessparameter, um die gewünschte Dünnwandgeometrie zu erreichen und gleichzeitig die strukturelle Integrität und Oberflächenqualität aufrechtzuerhalten. Die Implementierung von Echtzeit-Überwachungs- und Kontrollsystemen minimiert Defekte weiter und gewährleistet eine gleichbleibende Produktion hochwertiger Komponenten.
Multimaterial-Druckguss
Die Integration mehrerer Materialien in einem einzigen Druckgussteil eröffnet spannende Möglichkeiten zur Verbesserung von Funktionalität und Leistung. Dieser Ansatz ermöglicht die Kombination von Materialien mit unterschiedlichen Eigenschaften wie Festigkeit, Wärmeleitfähigkeit und elektrischer Leitfähigkeit in einem einzigen Teil. So könnte ein Bauteil beispielsweise einen Kern aus hochfester Aluminiumlegierung für die strukturelle Integrität enthalten, kombiniert mit einem weicheren, dehnbareren Material in bestimmten Bereichen, um die Funktionalität zu verbessern oder den Verschleiß zu verringern. Dies erfordert ein ausgeklügeltes Formdesign und eine präzise Kontrolle des Spritzvorgangs, um eine genaue Platzierung und Verbindung der verschiedenen Materialien sicherzustellen.
Bei fortgeschrittenen Techniken im Mehrmaterial-Druckguss werden häufig spezielle Einsätze in der Form verwendet, um die Grenzen verschiedener Materialien zu definieren. Eine genaue Kontrolle der Einspritzparameter ist entscheidend, um ein Vermischen oder Delaminieren der verschiedenen Materialien zu verhindern. Der Einsatz von Simulationssoftware ist besonders wichtig, um die Design- und Prozessparameter zu optimieren und die erfolgreiche Integration und Verbindung mehrerer Materialien im Endprodukt sicherzustellen. Die Entwicklung neuer Verbindungstechniken wie Reibrührschweißen oder Diffusionsschweißen spielt ebenfalls eine wichtige Rolle bei der Herstellung robuster und zuverlässiger Mehrmaterial-Gussteile.
Fortschrittliche Matrizenmaterialien und Beschichtungen
Die Leistung und Langlebigkeit von Druckgussformen wirken sich erheblich auf die Gesamteffizienz und -qualität des Prozesses aus. Herkömmliche Formenmaterialien sind zwar funktionsfähig, weisen jedoch häufig Einschränkungen in Bezug auf Verschleißfestigkeit, Wärmeleitfähigkeit und Korrosionsbeständigkeit auf. Moderne Fortschritte konzentrieren sich auf die Entwicklung und Anwendung innovativer Formenmaterialien wie fortschrittliche Stahllegierungen, Keramikverbundstoffe und neuartige Beschichtungen. Diese Materialien bieten eine verbesserte Haltbarkeit und ermöglichen höhere Produktionsraten und eine längere Lebensdauer der Formen.
Spezielle Beschichtungen, die auf die Oberfläche der Gussform aufgetragen werden, erhöhen die Verschleißfestigkeit zusätzlich, verringern die Reibung und verbessern die Oberflächenbeschaffenheit der Gussteile. Diese Beschichtungen können auf bestimmte Anwendungen zugeschnitten werden und bieten maßgeschneiderte Eigenschaften wie verbesserte Wärmeübertragung oder Freisetzungseigenschaften. Die Entwicklung haltbarerer und zuverlässigerer Beschichtungen läuft weiter, wobei der Schwerpunkt auf einer noch höheren Verschleißfestigkeit und einer Verbesserung der Gesamtqualität der Gussteile liegt. Dies ermöglicht höhere Produktionsraten und eine verbesserte Komponentenqualität bei gleichzeitiger Minimierung der Ausfallzeiten im Zusammenhang mit der Wartung und dem Austausch der Gussform.